Rizoma. Quando il Made in Italy è un valore aggiunto
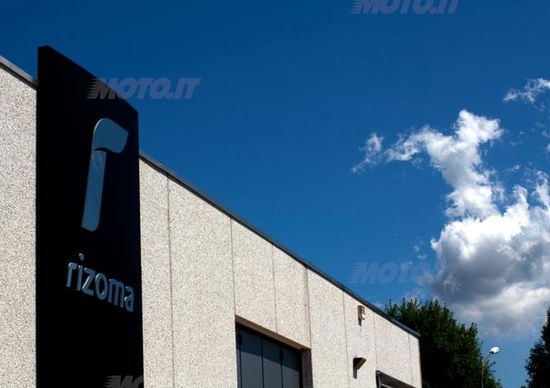
Un 2011 ricco di novità per Rizoma, a partire dal nuovo logo, che richiama in maniera evidente il componente principe utilizzato dall'azienda, che per chi ancora non lo sapesse è l'alluminio, materiale da cui nascono tutti i componenti dell'azienda di Ferno in provincia di Varese.
Rizoma nasce nel 1997 grazie alla intraprendenza di due fratelli, Fabio e Fabrizio Rigolio, che mettendo a frutto l'esperienza famigliare nelle lavorazioni meccaniche, iniziano a produrre componenti per moto. Dopo quasi tre lustri, l'offerta di prodotti passa da pochi componenti agli attuali 1300 accessori, presentati nel nuovo catalogo 2011, un vero e proprio libro di 300 pagine pensato e realizzato con cura ed estremamente elegante nella veste. Sembra tutto tranne che un catalogo di accessori.
Oltre alla gamma di prodotti il passare degli anni porta ad un incremento del fatturato, si passa dal milione di Euro del 2001 ai 12 attuali, mentre i dipendenti passano ad essere ben 50, un bella crescita se si pensa che inizialmente erano solo 5. Lavorare bene e con passione paga.
Crisi o non crisi, Rizoma continua crescere, e i suoi accessori per le moto vengono venduti in circa 30 paesi sparsi per il mondo. Il segreto di questo successo è da attribuire alla qualità dei prodotti, una ricerca quasi maniacale della perfezione, a cui abbiamo assistito durante una visita guidata dell’azienda, caratterizza ogni singolo particolare che viene progettato e realizzato da Rizoma. Ricerca e sviluppo sono costanti, basti pensare che ben il 6% del fatturato viene investito in questi due campi. Percentuale da azienda che opera nel campo famacologico piuttosto che della lavorazione meccanica, dove in media ci si ferma a 2/3%.
L'attenzione e la cura per ogni singolo particolare, la tocchiamo con mano e la osserviamo direttamente durante la visita guidata lì dove i componenti Rizoma prendono forma.
Accompagnati da Davide Soffiantino (Italy Sales Manager) assistiamo alla fresatura di decine di billet di alluminio, che magicamente, o meglio meccanicamente, prendono forma, attraverso il millimetrico e incessante lavoro compiuto dai tornii e dalle frese a quattro assi. Gli scarti di lavorazione naturalmente vengono riciclati, non da Rizoma, ma da un’azienda esterna. Il pezzo così fresato, passa poi alla macchine per la burattatura, che in parole povere assomigliano a dei grossi pentoloni ricolmi di coni, di varie dimensioni, solitamente in ceramica (ma possono anche essere di plastica o addirittura legno) all’interno dei quali vengono immersi i pezzi in lavorazione. Questi vengono “rimescolati” per un periodo di tempo che può variare da 8 fino a 48 ore, per far sì che ogni traccia di lavorazione, le bave metalliche tanto per intenderci, venga completamente levigata. Una volta terminata la burattatura, i pezzi vanno anodizzati (attraverso un riporto superficiale di ossido di alluminio) e acquisiscono quindi le diverse colorazioni) questa operazione è affidata ad una azienda esterna specializzata, che garantisce la massima qualità in questo tipo di lavorazione. Questo è un passaggio molto importante, perché di fatto l’anodizzazione, oltre a rendere più attraente il componente, protegge di fatto il metallo dagli agenti atmosferici evitando che possa “fiorire”, e un’ anodizzazione fatta come si deve non perde le proprie caratteristiche (ed anche il colore…) per svariati anni. Qui in Rizoma garantiscono una longevità che nel peggiore dei casi è di 8 anni, ma arriva fino a 12/15, ma in condizioni d’uso estreme, difficilmente riscontrabili nell’utilizzo comune della moto.
Una volta che il pezzo rientra, viene stoccato nei magazzini di stazionamento in attesa che il Direttore di produzione dia gli ordini di assemblaggio e, particolare importantissimo, marchiato, con scrittura laser. Oltre al marchio Rizoma, viene impresso anche il numero di lotto produttivo in modo da conferirgli la necessaria rintracciabilità (e mettere il bastone tra le ruote agli immancabili cloni asiatici).
Fatto e finito il componente deve essere confezionato. Fino all’anno scorso il confezionamento consisteva nel solo “sottovuoto”, mentre ora dopo un intero anno di studio sul packaging e l’estetica, e iniziando la collaborazione con un’azienda che produce per il settore della gioielleria e della cosmetica, si è arrivati alla confezione definitiva, una scatola particolarmente elegante, con una spugna interna tagliata al laser per riporre e proteggere i componenti nel migliore dei modi, come se fossero dei veri e propri gioielli. A garantire ulteriormente la qualità e l’originalità del componente, vengono posizionati dei sigilli di sicurezza che assicurano l’eventuale cliente sulla provenienza del prodotto.
Ma da dove si parte per definire i pezzi da costruire e il loro design.
Quest’ultimo viene sviluppato nella “White Box”, un cubo bianco, all’interno del fabbricato dove si svolgono le fasi di lavorazione, interdetta in particolare ai giornalisti, e dove viene effettuata la ricerca e sviluppo. Qui designer e tecnici pensano e mettono le basi per la produzione futura, utilizzando anche i dati dimensionali ricavati da uno scanner tridimensionale, che misura in tutto e per tutto la moto su cui si sta pensando di “intervenire”. I dati vengono poi passati al server della “White Box”, ed il lavoro può così avere inizio.
Una volta definito il design e la relativa matematica, si passa alla realizzazione del pezzo in resina, con una macchina che è in pratica una stampante laser tridimensionale, e che realizza il manichino.
A questo punto e dopo aver visto i vari passaggi della lavorazione, la tanta decantata precisione di lavorazione e facilità di montaggio vantata dai componenti Rizoma è diventata una certezza.
La prossima volta che toccherete con mano o semplicemente ammirerete degli accessori Rizoma, siamo certi che lo farete con occhi diversi, e ripenserete a quanto lavoro e impegno sono stati necessari per realizzarli … in Italia, un valore aggiunto.