Pregevolezza tecnica o riduzione dei costi?
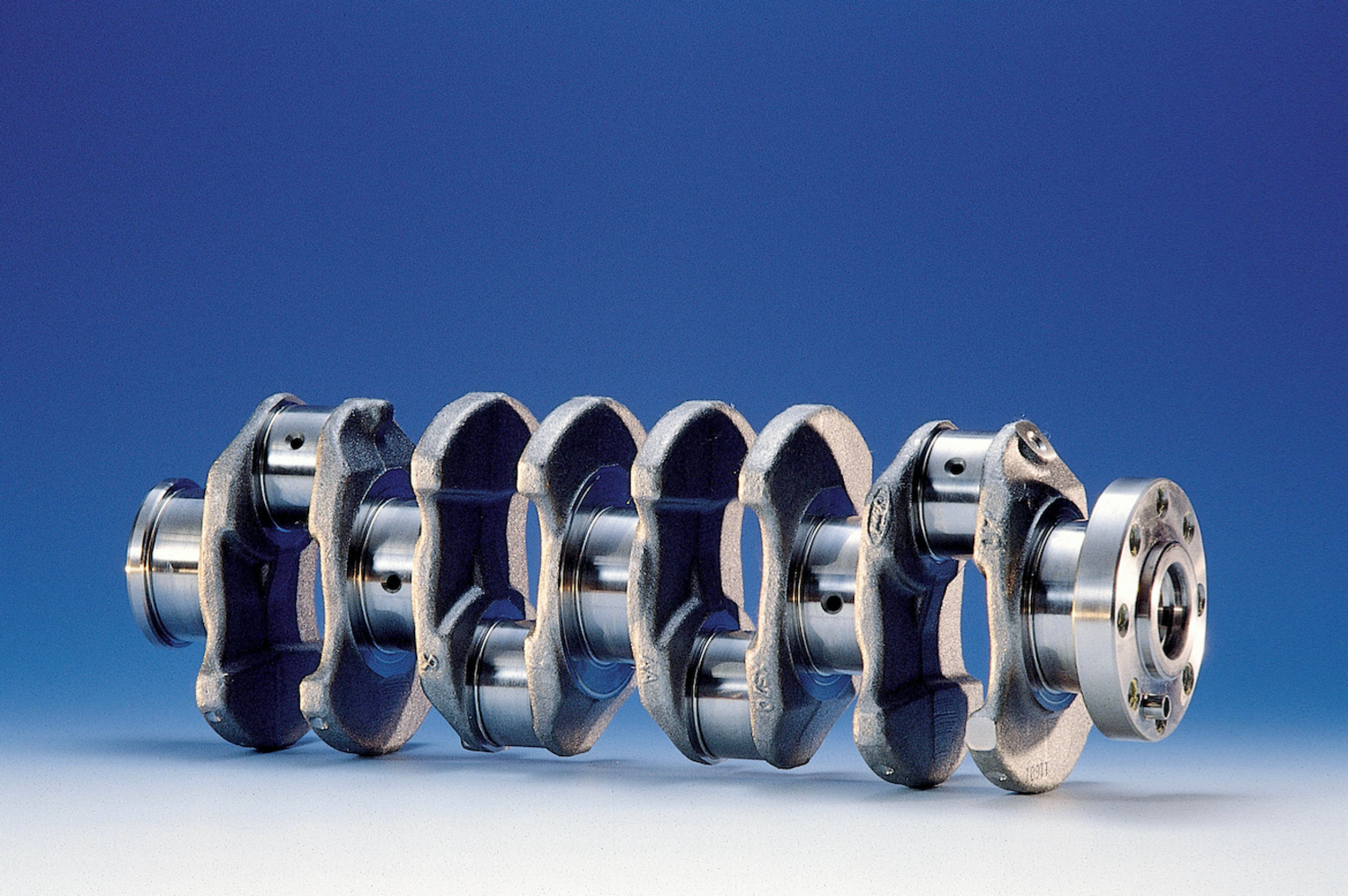
Da tempo uno dei principi fondamentali nel disegno e nello sviluppo dei motori e dei loro componenti prevede l’impiego solo di ciò che serve per raggiungere gli obiettivi previsti in termini di prestazioni, consumi, affidabilità e durata. Per rendere l’idea, questo significa che se una medesima cosa può essere ottenuta in due modi diversi, verrà sempre scelto quello meno costoso.
In fase di progetto, e poi di sviluppo e di industrializzazione, si agisce in più modi. Tanto per cominciare ci sono le scelte che riguardano i materiali da utilizzare per i vari componenti. Alcuni di questi ultimi, come le bronzine, i pistoni e le valvole, non sono realizzati in casa ma vengono prodotti da fornitori esterni; il discorso comunque è sempre lo stesso.
Fino a non molto tempo fa si utilizzavano i materiali “usuali”, cioè quelli che erano stati impiegati per i modelli precedenti, per i quali andavano sicuramente bene. Negli ultimi anni però la situazione è cambiata. Le prestazioni dei motori sono aumentate (fondamentalmente per via della sovralimentazione) e con loro le sollecitazioni alle quali sono sottoposti gli organi meccanici; inoltre ci sono state interessanti novità da parte delle industrie che forniscono i materiali di partenza alle fonderie e ai reparti di forgiatura.
Un esempio significativo ci viene dato dagli acciai microlegati, che consentono una notevole riduzione dei costi di produzione di parti come gli alberi a gomiti rispetto agli acciai impiegati in precedenza. Dunque per ciascun componente in ufficio tecnico si valutano le varie possibilità e si consultano la fonderia, l’officina di stampaggio e i fornitori esterni (di materiali e di pezzi finiti). Quello che si cerca anche in questo caso è in fondo il miglior rapporto tra le prestazioni, ovvero la qualità, e il prezzo.
Le leghe di alluminio sono molto numerose e hanno caratteristiche diverse una dall’altra. Si dividono in quelle da lavorazione plastica, che non hanno particolare interesse in campo motoristico, e quelle da fonderia, la cui colabilità varia a seconda dei casi (come pure il costo…).
Le teste dei motori automobilistici sono tutte in lega di alluminio; questa famiglia di materiali abbina una ridotta densità a una elevata conduttività termica e consente l’impiego di qualunque tecnica fusoria; quella adottata varia a seconda dei casi, in base anche alle strutture produttive disponibili. Per le teste, a differenza di quanto avviene per i cilindri e i basamenti, la pressofusione non può essere però impiegata in quanto non consente la realizzazione di cavità interne, ovvero di intercapedini per il passaggio dell’acqua. Nella produzione di serie il procedimento più utilizzato per tali componenti è la fusione in conchiglia; di recente sta trovando un certo impiego anche il processo denominato lost-foam, con modello a perdere in polistirene espanso e stampo in sabbia.
Non solo il tipo di materiale è importante, ma anche quanto se ne impiega! Anni fa una grande casa diminuì di due decimi di millimetro lo spessore delle rondelle piazzate sotto le teste delle principali viti. Sembra una cosa da nulla, ma moltiplicando il materiale risparmiato per milioni di pezzi il vantaggio economico non è proprio trascurabile.
Sia la ghisa che l’acciaio sono leghe ferrose. Hanno caratteristiche notevolmente diverse e si differenziano per il contenuto di carbonio. In effetti si tratta di due grandi famiglie di materiali, disponibili in numerosi tipi con varie microstrutture; spesso contengono anche determinate quantità di elementi aggiuntivi differenti (cioè di “leganti”).
Le ghise hanno una resistenza a trazione nettamente inferiore, rispetto agli acciai. Inoltre sono meno tenaci e resilienti e hanno un modulo elastico notevolmente più basso.
I componenti in ghisa si ottengono solo per fusione mentre quasi tutti quelli in acciaio vengono realizzati per forgiatura (stampaggio a caldo). Le ghise sferoidali si differenziano dalle comuni ghise grigie a livello di microstruttura, in quanto le particelle di grafite in esse presenti (e assenti invece negli acciai) hanno una forma diversa; hanno un costo maggiore ma le loro caratteristiche meccaniche sono superiori.
Ciò consente di impiegarle per gli alberi a gomiti destinati a motori di serie non molto spinti, con notevole vantaggio economico rispetto ai classici acciai. Questi ultimi però rimangono complessivamente superiori; in effetti sono gli unici materiali che possono venire utilizzati per gli alberi molto sollecitati, ovvero quelli dei motori di alta potenza specifica.
Gli elementi leganti che vengono aggiunti agli acciai sono principalmente il cromo, il nichel e il molibdeno, importantissimi ai fini delle caratteristiche meccaniche; purtroppo però sono costosi…
Per questa ragione di recente hanno conquistato una notevole popolarità gli acciai microlegati, che contengono quantità molto modeste di tali elementi e hanno quindi un costo contenuto (a ciò si aggiunge il vantaggio di non richiedere trattamenti, dopo lo stampaggio e le lavorazioni).
Anche i sistemi di produzione, che vengono stabiliti in fase di progetto, hanno una notevole importanza sotto l’aspetto economico. Per fare un esempio, non sono pochi i basamenti per i quali è stata scelta una struttura open-deck non tanto per ragioni puramente tecniche quanto per poterli realizzare mediante pressofusione.
In merito alle lavorazioni meccaniche, occorre innanzitutto sottolineare che i costi aumentano esponenzialmente man mano che si adottano tolleranze dimensionali e geometriche più ristrette (ciò contribuisce a spiegare l’elevatissimo prezzo dei motori da competizione). Dunque, anche qui entra in gioco il principio secondo il quale non si deve impiegare ciò che, ai fini delle prestazioni richieste e della durata, non è strettamente necessario.
In altre parole, nella produzione di serie non conviene realizzare componenti con una precisione talmente spinta da determinare costi molto elevati, quando lavorazioni leggermente meno accurate risultano comunque adeguate ai fini della funzionalità e della durata. In seguito alle dilatazioni termiche e/o alle sollecitazioni meccaniche i perni e i supporti possono scostarsi dal perfetto allineamento in misura maggiore di quella determinata, in condizioni statiche e a temperatura ambiente, dalle tolleranze di lavorazione… Considerazioni analoghe valgono anche per la finitura superficiale dei vari organi meccanici.
Naturalmente quando si tratta di motori da competizione o di altissime prestazioni la situazione è diversa: le considerazioni economiche sono meno importanti e la diminuzione degli attriti diventa vitale.
Pure il numero delle lavorazioni influisce pesantemente sui costi e quindi si cerca di ridurlo al minimo. Importa anche la quantità di materiale che deve essere rimosso.
Il costo delle parti fuse è minore di quello delle parti ottenute per forgiatura anche per questa ragione.
-
fabio2101, Pordenone (PN)Articoli sempre interessanti e istruttivi. Interessanti e quantomeno stimolanti molte informazioni che possono accendere la curiosità su rotture, usure precoci...e perché no anche CASI INSPIEGABILI che avvengono sui prodotti di serie che tutti noi guidiamo. Piacerebbe un analisi o parere personale dell'Ing Clarke sulle soluzioni applicate alle attuali supersportive 1000. Dato l'incremento esponenziale delle prestazioni, della ricerca dell'abbassamento dei costi e alla luce delle rotture più o meno note, mi incuriosisce sentire secondo l'Ing Clarke dove pende l'ago della bilancia...Marginalità o qualità? Vi sono errori progettuali dovuti alla necessità di ridurre i tempi di industrializzazione e sviluppo? Non chiedo di puntare il dito esplicitamente ma un semplice parere personale. Complimenti ancora per gli articoli.