Ogni cosa al posto giusto per un motore a punto
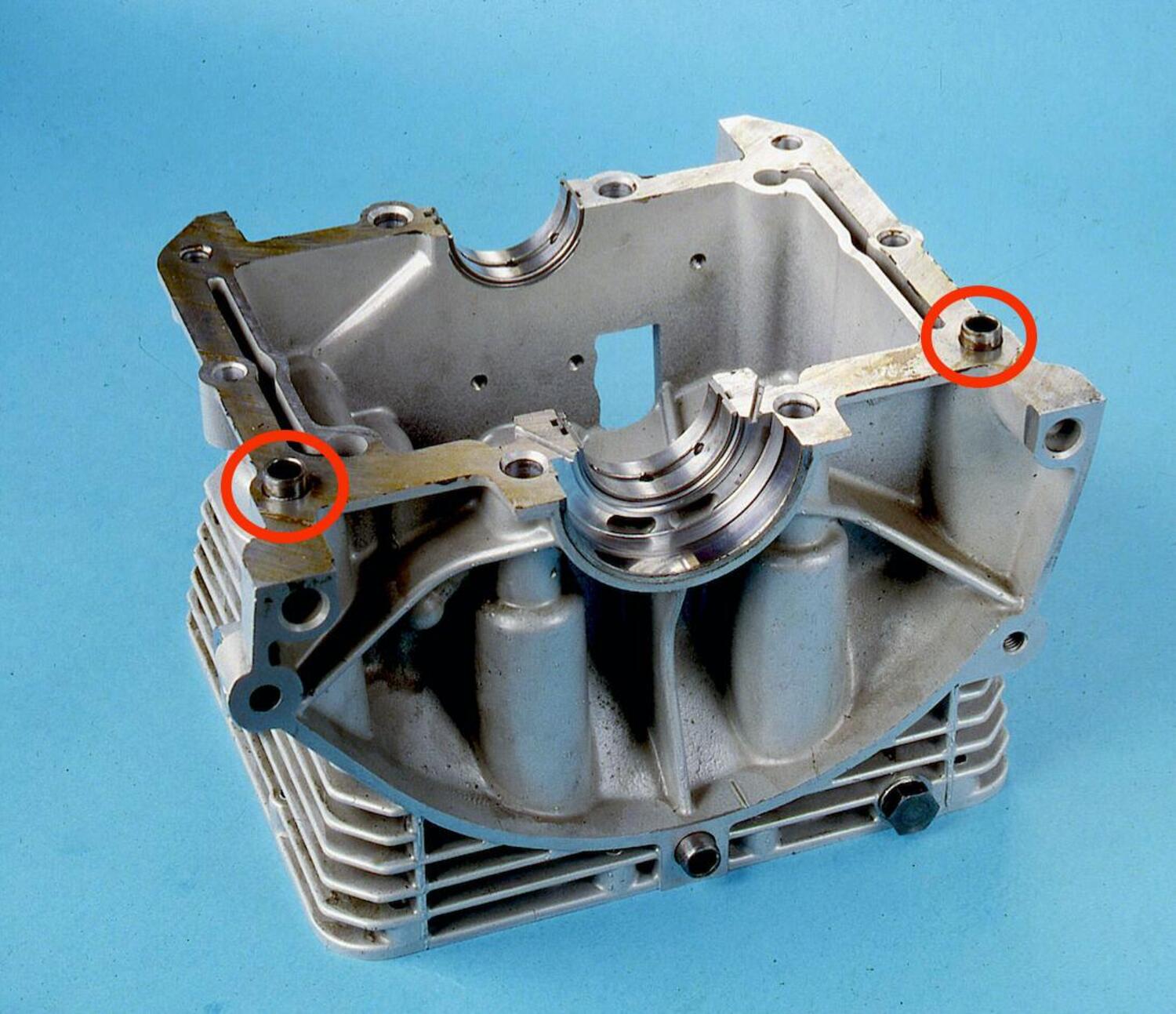
Gli organi meccanici devono essere lavorati con grande precisione sia dimensionale che geometrica.
Ciò però non basta. Devono anche essere collocati nella posizione corretta e con grande accuratezza. Ha poco senso infatti realizzare componenti con quote e forma il più possibile vicine a quelle ideali se poi essi non vengono piazzati esattamente dove devono. Si pensi a un albero a gomiti con perni di banco allineati con grande precisione; se viene installato su supporti non perfettamente coassiali è una catastrofe. Se va bene, ma proprio bene, aumenta solo l’attrito…
Ma come può verificarsi questa situazione se i semicarter nei quali sono ricavati i supporti sono stati lavorati rispettando le tolleranze prescritte dal progettista? Semplice, basta che essi non siano posizionati uno rispetto all’altro con la dovuta precisione.
Le viti servono per fissare i componenti, non per posizionarli. Tra il loro gambo e il foro nel quale si inserisce esiste inevitabilmente un certo gioco. Si potrebbe pensare di eliminarlo, realizzando fori e gambi delle viti con tolleranze dimensionali ristrettissime. A parte però il fatto che i costi diventerebbero inaccettabili, in pratica la cosa non sarebbe neanche fattibile. Lo smontaggio e il rimontaggio sarebbero impossibili.
Prendendo ad esempio un coperchio laterale e il basamento, qualche lieve errore di allineamento dei fori sarebbe inevitabile. E questo vale anche per la distanza tra gli assi dei fori praticati nei due componenti. Il coperchio laterale può essere posizionato con estrema precisione rispetto al basamento ma è impossibile che tutti i fori delle due parti in questione siano perfettamente allineati tra loro.
Dunque, tra il gambo delle viti e i fori praticati nelle due parti da unire esiste un lieve gioco. In diversi casi la scarsa accuratezza di posizionamento che si può ottenere in questo modo può comunque andare bene ma in altri non è accettabile.
Ci vuole una precisione maggiore.
È questo il caso tipicamente dei coperchi nei quali sono montati uno o più cuscinetti, che devono risultare perfettamente allineati con quelli installati nel basamento.
Per il fissaggio del cappello di alcune teste di biella si impiegano due viti che si inseriscono di precisione, ossia senza gioco, in fori essi pure calibrati. La soluzione però è costosa e non si presta a frequenti montaggi e smontaggi. Va bene solo per quel tipo di impiego.
Per posizionare con elevata precisione uno rispetto all’altro due componenti in genere si impiegano due boccole calibrate o spine (ovvero “grani”), che vengono installate con lieve forzamento in fori la cui disposizione è accuratamente studiata.
È questo tipicamente il caso dei due semicarter che costituiscono il basamento, sia che essi si uniscano secondo un piano verticale sia che lo facciano secondo un piano orizzontale. Qui la perfetta coassialità degli alloggiamenti dei cuscinetti di banco è assolutamente vitale (e lo stesso vale per quelli degli alberi del cambio).
Spine o bussole di posizionamento, ovvero di “centraggio”, si usano anche tra la testa e il cilindro e tra quest’ultimo e il basamento. In questi casi talvolta può essere sufficiente tra la bussola calibrata e il foro un accoppiamento “di precisione” (accurato ma senza interferenza, con montaggio agevolmente effettuabile a mano).
Sono centrati in questo modo anche i cappelli dei supporti divisi in due parti, come quelli di alcuni alberi a camme.
Davvero classico è il caso delle bielle. L’occhio della testa deve essere perfettamente rotondo e in corrispondenza delle superfici di unione con il cappello non ci devono essere scalini o discontinuità. Il cappello deve perciò essere posizionato con grande precisione. E dovrà essere disposto esattamente nella stessa posizione all’atto del rimontaggio.
I sistemi impiegati per ottenere questo sono svariati. Molto utilizzati sono quelli che prevedono rispettivamente l’impiego di viti con gambo calibrato o di una bussola di centraggio disposta coassialmente a ciascuna vite. Per le bielle destinate ai motori di prestazioni particolarmente elevate si impiegano spesso piccole spine calibrate (due per ogni cappello).
Negli ultimi anni si è andata diffondendo, raggiungendo una buona diffusione, la soluzione che prevede l’impiego di superfici di frattura coniugate: in fase di fabbricazione il cappello viene repentinamente separato dal corpo della biella con una rottura netta nelle zone predeterminate.
Si ottengono così delle superfici di unione microfrastagliate che assicurano un posizionamento estremamente preciso. Solo certi acciai si prestano però a questa frattura fragile localizzata.
Nelle bielle destinate ai motori da competizione si utilizzano talvolta dentature triangolari sulle superfici di unione, abbinate a piccole spine. Di recente però si sono affermate anche altre soluzioni più sofisticate.
Nel caso delle bielle, trattandosi di parti in movimento e sottoposte a ingenti forze sia d’inerzia che dovute alla pressione dei gas (che vanno ad aggiungersi a quelle centrifughe) occorre però fare i conti con sollecitazioni che nei motori di alta potenza specifica possono risultare molto elevate. Queste forze tendono a deformare l’occhio della testa e a spostare il cappello rispetto al corpo della biella. È dunque importante che il cappello stesso sia non solo centrato con la massima precisione ma che rimanga nella posizione corretta anche in presenza delle forti sollecitazioni in gioco.