Massimo Clarke: Introduzione alle sospensioni. Sesta Parte
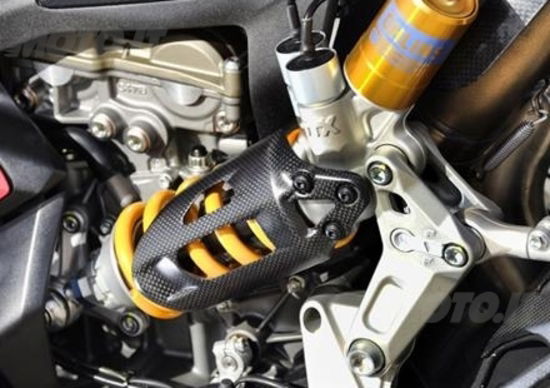
Da diversi anni a questa parte in molte moto il monoammortizzatore posteriore non collega direttamente il forcellone oscillante al telaio ma lo fa per mezzo di un leveraggio del tipo a biella e manovella, con quest’ultima che si muove secondo un arco di cerchio. In pratica si tratta di un sistema a quadrilatero deformabile nel quale la biella è vincolata al forcellone e la manovella è fulcrata, a una estremità o centralmente, nel telaio.
Il mono progressivo
Grazie a questo leveraggio, a mano a mano che la sospensione si comprime varia il rapporto tra lo spostamento della ruota e la compressione della molla, e quindi anche il movimento del pistone dell’ammortizzatore. Per fare un esempio, se all’inizio della escursione della sospensione un movimento della ruota di 2 mm determina una compressione del monoammortizzatore di 1 mm, verso la fine della escursione un eguale spostamento della ruota dà luogo a una compressione del “mono” di 1,25 mm. In questo caso è come se la rigidezza della molla fosse aumentata del 25%!
Dunque, all’aumentare del carico, e quindi della compressione del gruppo molla-ammortizzatore, la sospensione diventa sempre più rigida. Quando si impiega un collegamento diretto, ossia lineare, se la molla è a passo costante, perfettamente cilindrica e con il diametro del filo che non varia per tutta la lunghezza, il grafico che rappresenta il rapporto tra la forza esercitata dalla molla stessa e lo spostamento della ruota è una retta con una certa inclinazione. Se si impiega un leveraggio articolato, esso diventa una curva, che tende a “impennarsi” nel tratto finale. Questo nel caso di un leveraggio di tipo progressivo, come nella quasi totalità dei casi (esistono comunque anche alcuni esempi di leveraggi regressivi).
È importante osservare che l’impiego di questi sistemi articolati, noti anche come VLRS (Variable Leverage Rear Suspension) ha una sensibile influenza anche sulla funzione ammortizzante. Man mano che la sospensione si comprime, per una stessa escursione della ruota si ha un maggiore spostamento del pistone dell’ammortizzatore. Se si fa riferimento a ciò che accade nell’unità di tempo, è chiaro che cambia anche il rapporto tra la velocità del pistone dell’ammortizzatore e la velocità con la quale si sposta la ruota. Dunque, non aumenta solo la forza necessaria per comprimere la molla, ma anche la frenatura idraulica. E l’ammortizzatore non è più solo speed sensitive, ma diventa anche position sensitive, come la molla.
L’idea che ha portato alla realizzazione dei sistemi VLRS è quella di ottenere una sospensione “tenera” quando il movimento della ruota è modesto, ovvero quando si incontrano piccole asperità, e di avere una sospensione più rigida quando si incontrano asperità molto accentuate (e la compressione della sospensione stessa è maggiore). I sistemi di questo genere effettivamente possono essere in grado di “modellare” la risposta della sospensione, almeno in una certa misura.
Gli schemi base con i quali sono realizzati i leveraggi articolati sono fondamentalmente tre. L’ammortizzatore può essere piazzato tra la manovella e il forcellone, tra il telaio e la biella o tra il telaio e la manovella. Riferendosi a uno o a entrambi gli elementi del leveraggio i piloti e i tecnici parlano generalmente di “link”.
La forcella, meglio rovesciata
Le forcelle impiegate sulle moto di elevate prestazioni sono del tipo a steli rovesciati, caratterizzato da una rigidezza notevolmente maggiore rispetto a quello tradizionale. Come gli ammortizzatori, anche questi componenti sono stati oggetto negli ultimi anni di importanti miglioramenti. Principalmente si è lavorato per incrementare la rigidità e la scorrevolezza. La presenza dei paraoli, dei parapolvere e l’attrito tra le parti mobili e quelle fisse (cioè i foderi) determinano una certa resistenza al movimento delle canne. In particolare, sono la resistenza iniziale e quella che si incontra quando i movimenti sono di modesta entità che possono creare fastidi. In presenza di notevoli carichi laterali occorre evitare che si possano verificare fenomeni del tipo “stick then slip”. Come ovvio, eventuali flessioni delle canne sono nocive in quest’ottica, in quanto aumentano la resistenza al moto. Per migliorare al massimo la scorrevolezza si impiegano finiture superficiali elevate, si curano con attenzione gli accoppiamenti, si adottano tolleranze dimensionali e geometriche molto ridotte, e si applicano sulle canne riporti con un basso coefficiente di attrito (il più noto è il TiN, cioè il nitruro di titanio, depositato con tecnologia PVD). Importanti sono anche l’uso di paraoli di ultima generazione, a basso attrito, e quello di boccole impregnate con lubrificante solido.
Per aumentare la rigidezza si è lavorato a livello di canne e di dimensioni e disegno delle piastre. Di queste ultime è l’inferiore a essere maggiormente sollecitata; per questo motivo in genere è più spessa di quella superiore. Per quanto riguarda le canne, è ovvio che un diametro maggiore risulta vantaggioso ai fini della rigidezza. Occorre comunque osservare che se la forcella è particolarmente rigida, alcuni piloti lamentano una perdita di feeling con l’avantreno, almeno in certe condizioni di impiego. Per questa ragione vengono realizzate forcelle dello stesso modello con canne di diametri differenti e sono disponibili, per una stessa forcella, piastre diverse.
Le forcelle svolgono la stessa funzione elastica e smorzante che posteriormente svolge il gruppo molla-ammortizzatore. Funzionano in maniera analoga, ma con alcune differenze di non poco conto. Gli steli sono inclinati e non verticali. Questo vuol dire che, per un dato spostamento verso l’alto della ruota, le molle si comprimono in misura maggiore di quanto farebbero se la forcella fosse, per ipotesi, verticale. Inoltre, all’interno di ciascuno stelo, al di sopra dell’olio, c’è aria. Quando la compressione della forcella diventa considerevole, alla forza della molla va a sommarsi una vera e propria assistenza pneumatica. Il livello dell’olio ha quindi una notevole importanza. Se esso è elevato, lo spazio a disposizione dell’aria, con la forcella a riposo, è ridotto e di conseguenza, quando la sospensione si comprime, l’intervento pneumatico risulta più vigoroso. Il contrario avviene, ovviamente, quando il livello dell’olio è più basso. Se ben regolata, l’assistenza pneumatica evita alla sospensione di “tamponare” a fine corsa e può avere un effetto benefico sulla progressività nella parte finale della compressione.
Le moderne forcelle sono pressoché invariabilmente del tipo a cartuccia, che abbina a una eccellente funzionalità una ampia possibilità di regolazioni. In pratica all’interno di ogni stelo viene piazzato un vero e proprio ammortizzatore a sé stante. Lo schema base prevede un tubo interno, dotato inferiormente di fori di collegamento al vano esterno, controllati da una valvola che regola il passaggio dell’olio in compressione, vincolata al piedino. Al tappo posto alla estremità superiore dello stelo è invece vincolata un’asta, che penetra nel tubo interno (cioè nella cartuccia) e termina nel pistone, dotato della valvola di estensione. Rispetto a questo schema base esistono diverse varianti, alcune delle quali vengono impiegate in forcelle destinate a moto di elevate prestazioni. Si hanno così cartucce sigillate e talvolta anche pressurizzate e altre raffinate variazioni sul tema.
-
alberto.ancillotti, Tavarnelle Val di Pesa (FI)Ciao Massimo,sono Alberto ancillotti, il sistema in foto è un PULL Shock come da mio brevetto del 1980
-
marty1e poi se la compressione del “mono” è diventata di 1,25 mm cioè 0.25 mm in più la rigidezza della molla dovrebbe essere diminuita non aumentata o no?